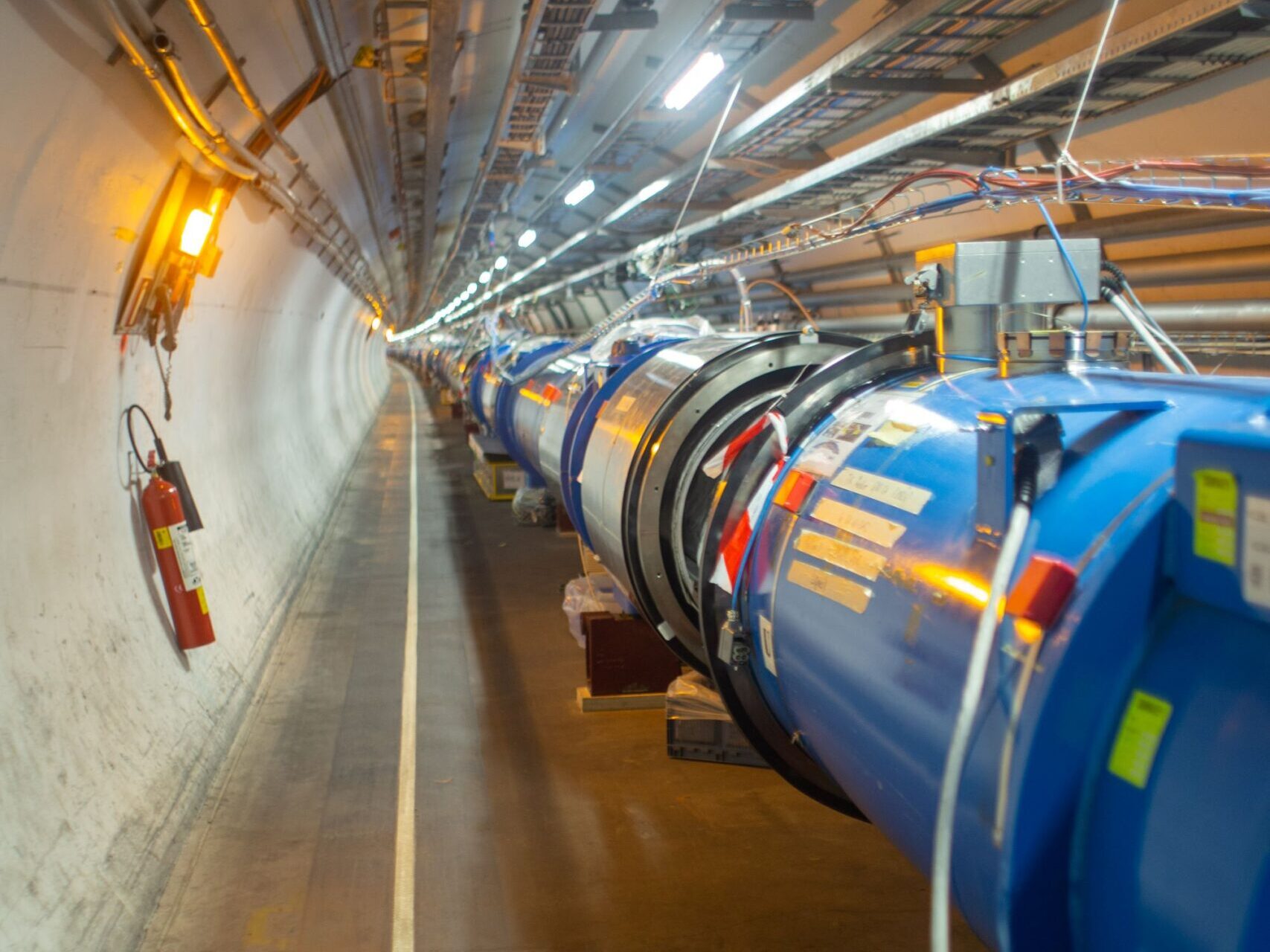
Capabilities of Niobium
With over 100 years of experience in manufacturing and developing refractory metals, Elmet Technologies actively offers expansive capabilities in niobium and its alloys, perfectly suited for various solutions. By utilizing advanced metallurgy processes, we achieve high-quality products. Consequently, these niobium materials significantly enhance properties and functionality, making them ideal for a wide range of applications in industries such as aerospace, electronics, nuclear power, and defense.
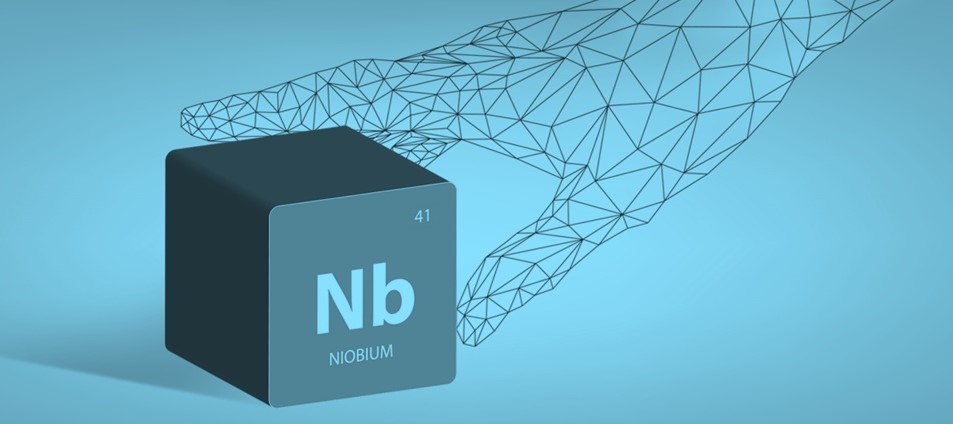
Moreover, when corrosion is a concern, niobium is a top choice due to its potential for reducing downtime and increasing equipment life, ultimately boosting profitability. The knowledgeable customer support team at Elmet is always available to collaborate with customers and develop niobium solutions tailored to their specific needs.
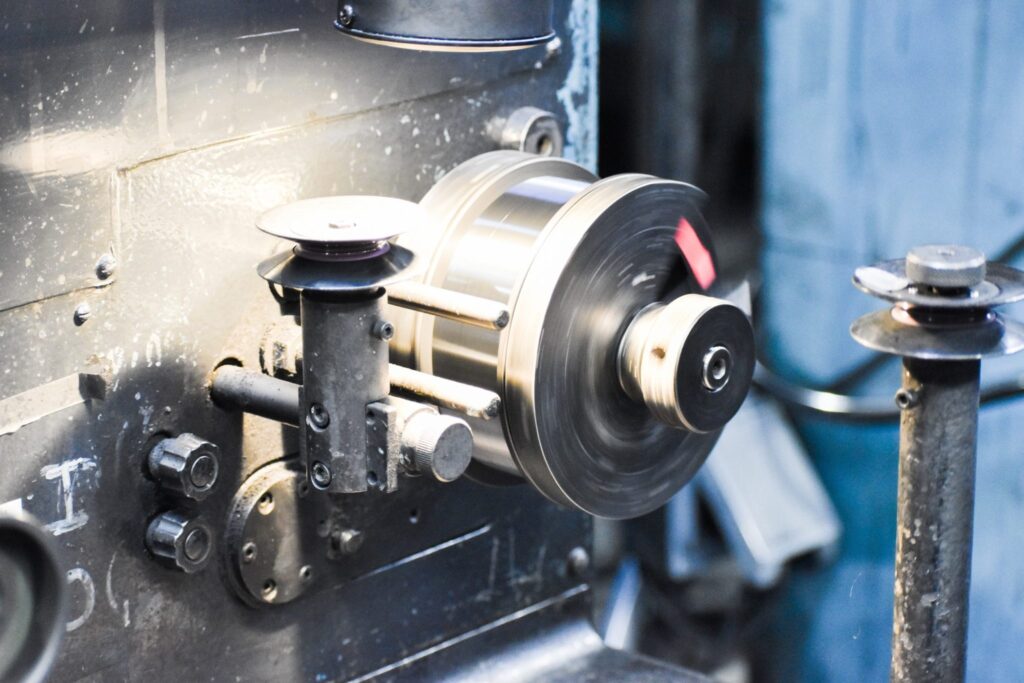
Niobium Machining Capabilities
With decades of experience in refractory metals, we proudly offer advanced niobium machining and fabrication capabilities.
By continuously refining our methods, we ensure that each project meets the highest standards.
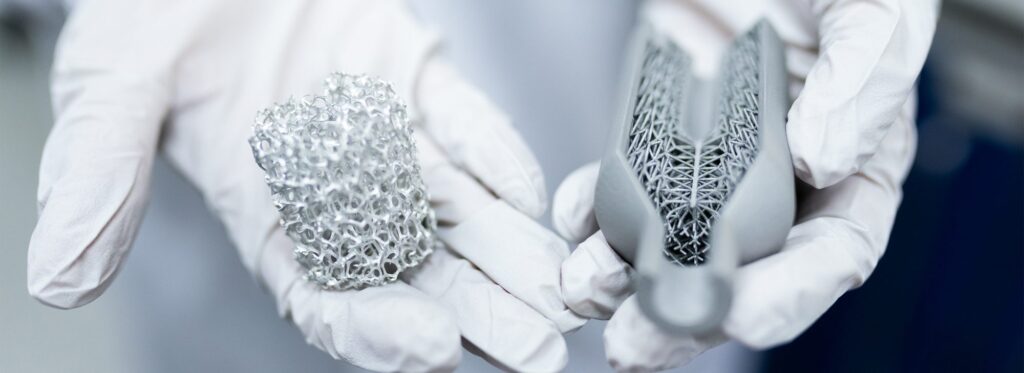
Niobium Capabilities In
Additive Manufacturing
The Additive Manufacturing (AM) industry has evolved as the preferred method for producing complex components with small geometries.
We proudly supply niobium for various AM projects as it paves the way for new production capabilities across markets.
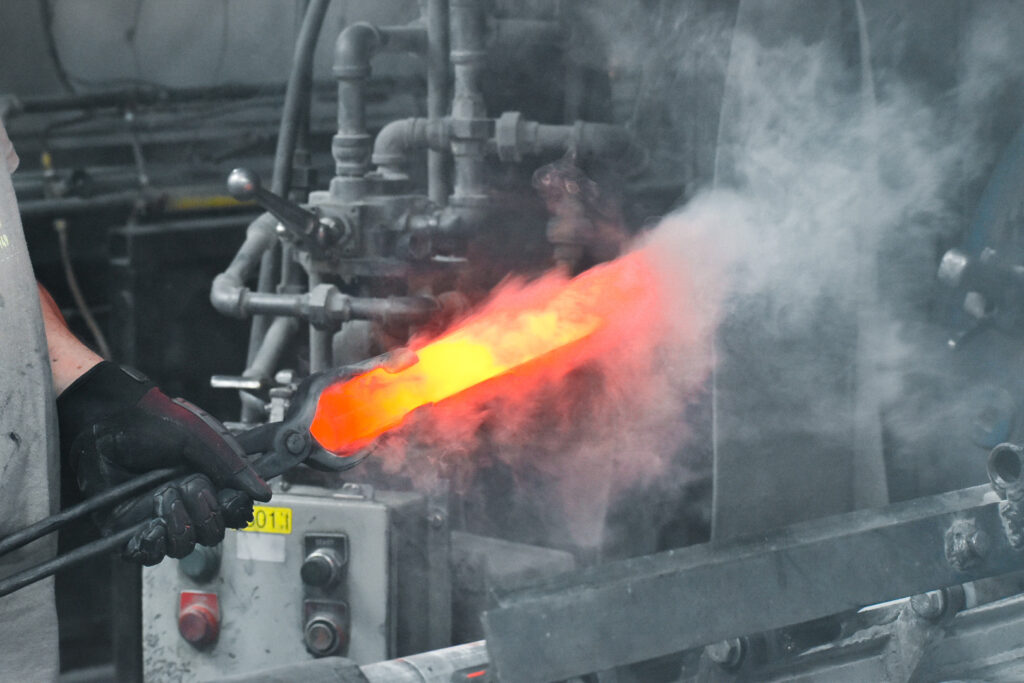
Rotary Forging capabilties
We leverage the advantages of toll processes by seamlessly managing a variety of project types.
We begin with material procurement, then move through billet preparation and forging, and finally advance to the final processing stage.
Advantages of Using Niobium
- Outstanding corrosion resistance
- High strength and stability even at elevated temperatures
- High ductility and toughness
- Superior thermal conductivity
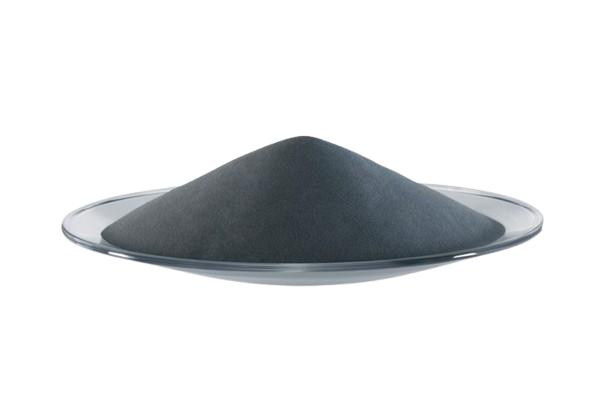
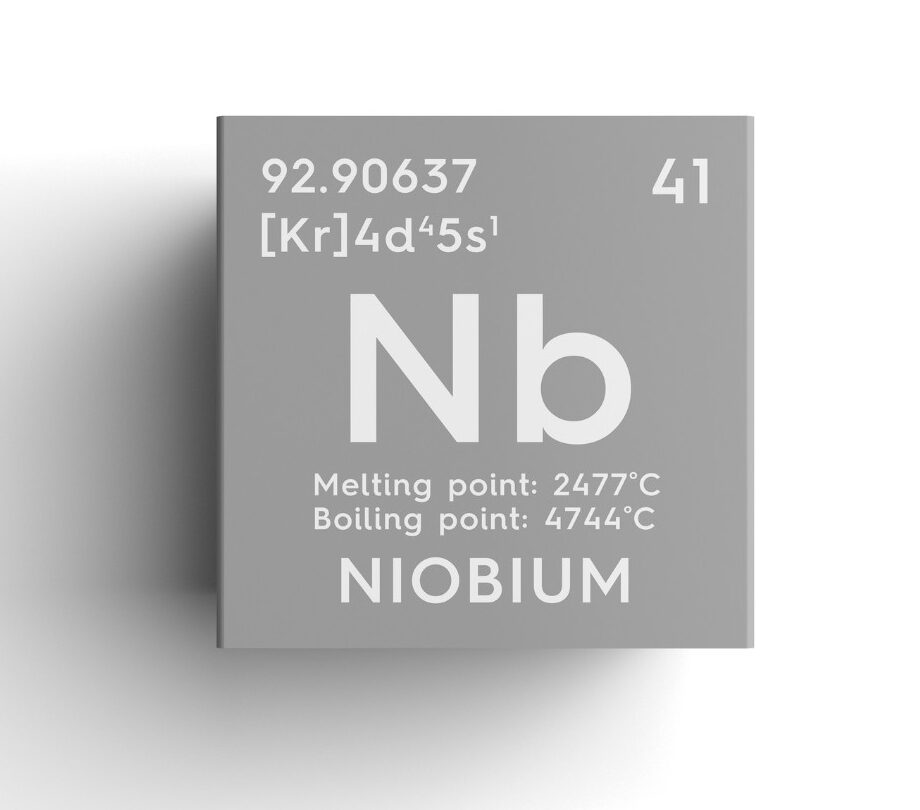
Chemical Resistance
Niobium remains nearly unaffected by chemical attacks, as it actively functions in the widest array of harsh oxidizing and reducing environments. It is resistant to a large group of harsh environments.
- Mineral acids
- Most organic acids
- Liquid metals
- Most salts
- Some fluoride-contaminated solutions
Niobium for Severe Environments
Elmet Technologies provides an extensive array of corrosion-resistant solutions for tackling the most challenging environments. Thanks to its corrosion resistance, durability, superior heat transfer properties, and workability, niobium is proven to be the ideal fabrication material for virtually any application within the pharmaceutical and chemical industries.
We actively employ niobium in the production of multi-purpose condensers, helical coils, pipe spools, and valve linings, along with various components that encounter corrosive fluids. Additionally, it plays a pivotal role in the creation of shell and tube heat exchangers, columns, and bayonet heaters.
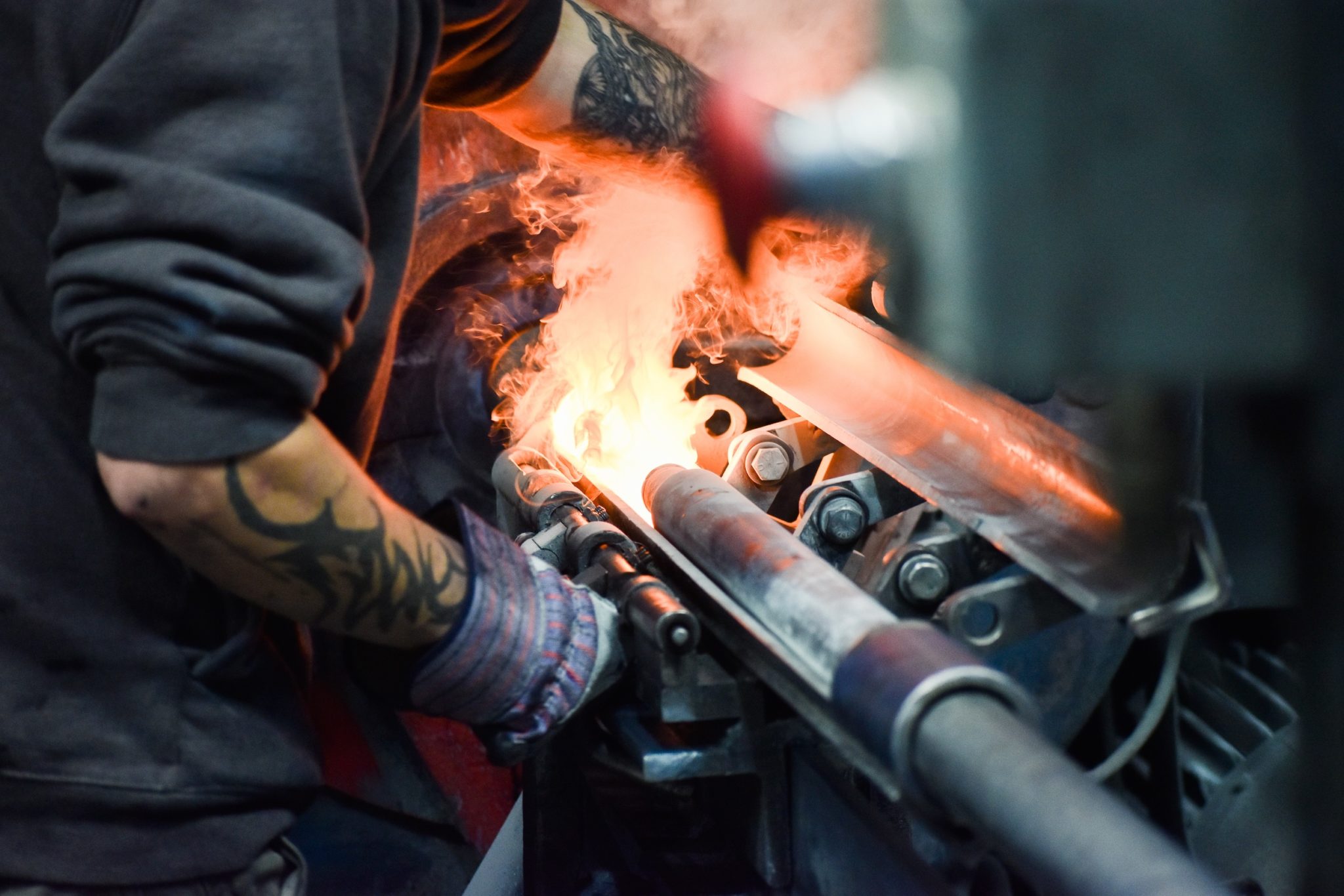
Typical Corrosive Applications
- Polycarbonates
- Silicones – via MethylChloride/HCI
- Isocyanates – TDI and/or MDI
- Nitrobenzene
- Bromine
- Bisphenol A
- MEK & IPA
- Acid Concentration
- Pickling
- Pharmaceuticals
Advancing Refractory Metals with Precision
As a global leader in refractory metals, Elmet Technologies operates cutting-edge laboratories where we continuously enhance and advance our products and materials.
- In-house expertise in forging, rolling, machining, cutting, and fabrication
- Chemical, mechanical, and microstructure monitoring in-house
- Expertise in thermal processing
- Consistent grain size and texture properties
Niobium Production Process
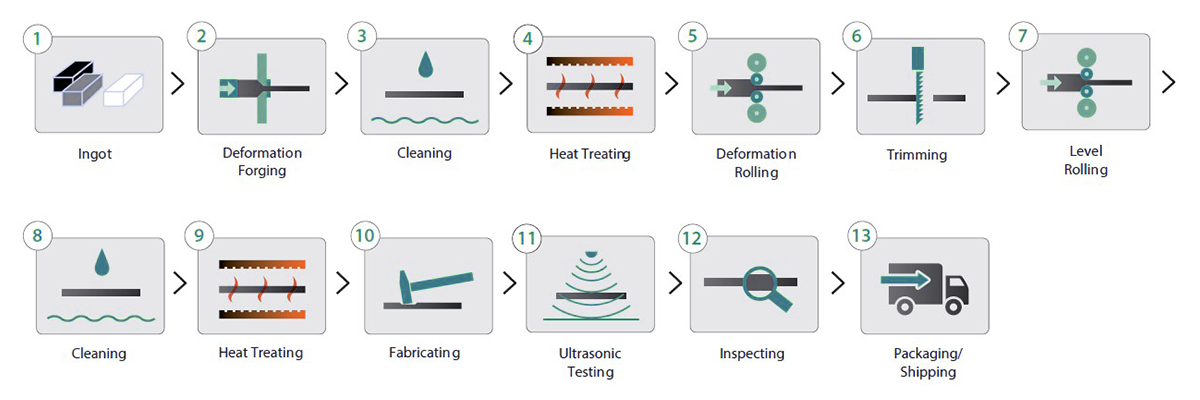
At Elmet, product quality is our top priority. We carefully oversee every stage of the production process, implementing rigorous quality programs to consistently deliver exceptional products. Our team of highly skilled technical experts brings deep expertise in materials and their applications, ensuring our development and manufacturing processes align with customer needs.
All Elmet Technologies facilities are ISO 9001 certified, and we adhere strictly to customer approval protocols, guaranteeing the highest standards in everything we deliver.
Forms and Tolerances
Form | Thickness, Diameter, Wall inches (mm) | Width, Length Inches (mm) |
Sheet | 0.005″ to 0.020″ (0.1270 to 0.50 mm) | 36″ max. width x coil (915 mm max. width x coil) |
Sheet | 0.015″ to 0.060″ (0.380 to 1.524 mm) | 40″ width x coil (1000 mm width x coil) |
Plate | 0.060″ to 0.125″ (1.524 to 3.175 mm) | Width not to exceed 40″ (1000 mm) Total weight of finished plate not to exceed 350 Ib. |
Rod | 0.125″ to 0.625″ (3.175 to 15.875 mm dia.) 0.625″ to 3.000″ dia. (15.875 to 76.200 mm dia.) | Coil or straight lengths straight lengths |
Ingot | > 3″ (76.2 mm) | Depending on weight |
Welded Tubing | 0.5″ OD x 0.015″ – 0.040″ wall (12.7 mm OD x 0.380 – 1.0 mm wall) 0.75″ OD x 0.015″ – 0.050″ wall (19.05 mm OD x 0.380 – 1.27 mm wall) 1.0 – 4.0″ OD x 0.015″ – 0.100″ wall (25.4 – 102 mm OD x 0.380 – 2.540 mm wall) |
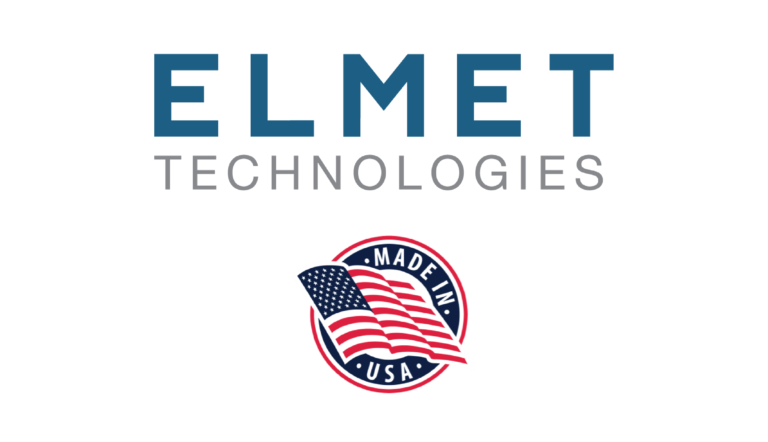
Six Sigma Capabilities of Niobium
Six Sigma, a methodology that enhances business processes through statistical analysis instead of guesswork, benefits greatly from the use of niobium. Customers aiming to achieve Six Sigma goals find niobium to be an excellent choice. Its attributes – purity, inertness, toughness, reliability, and robustness in diverse environments – make it ideal for those dedicated to implementing Six Sigma concepts.