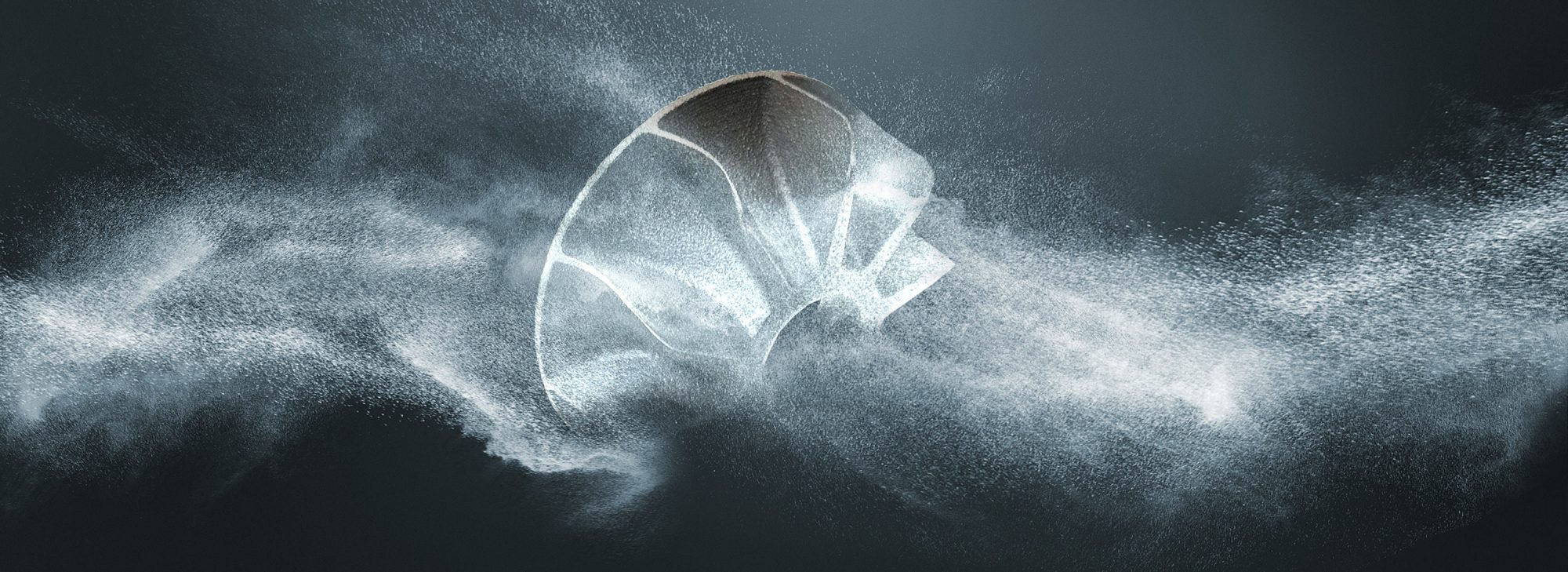
Niobium in Additive Manufacturing
Niobium in additive manufacturing (AM) is revolutionizing production capabilities across various markets. At Elmet Technologies, we are leveraging this innovation to push boundaries. Commonly referred to as 3D printing, AM originated as a groundbreaking innovation for polymer prototyping. Now, it has become essential for producing intricate components with small geometries from some of the most durable engineering materials.
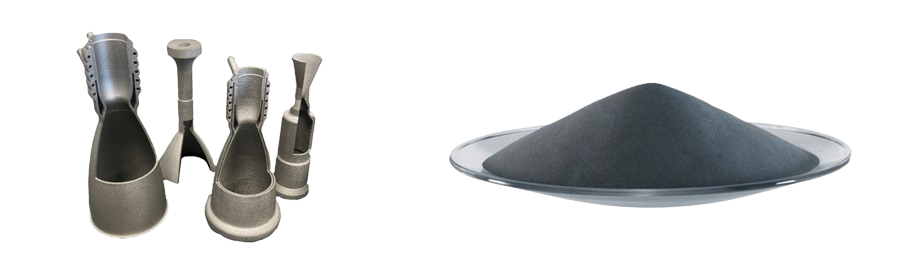
Elmet Technologies is investing heavily in cutting-edge AM technologies to complement our well-established refractory metal and alloy manufacturing expertise. Consequently, these two branches of our business align to significantly expand the range of products and services we provide to the additive manufacturing industry.
Markets that Use Niobium in Additive Manufacturing
Elmet Technologies’ refractory metal 3D printing solutions support customers in several critical markets. Our solutions enable each industry to benefit from the unique advantages of AM. Currently served markets and applications include: medical, nuclear, aerospace, defense, and industrial.
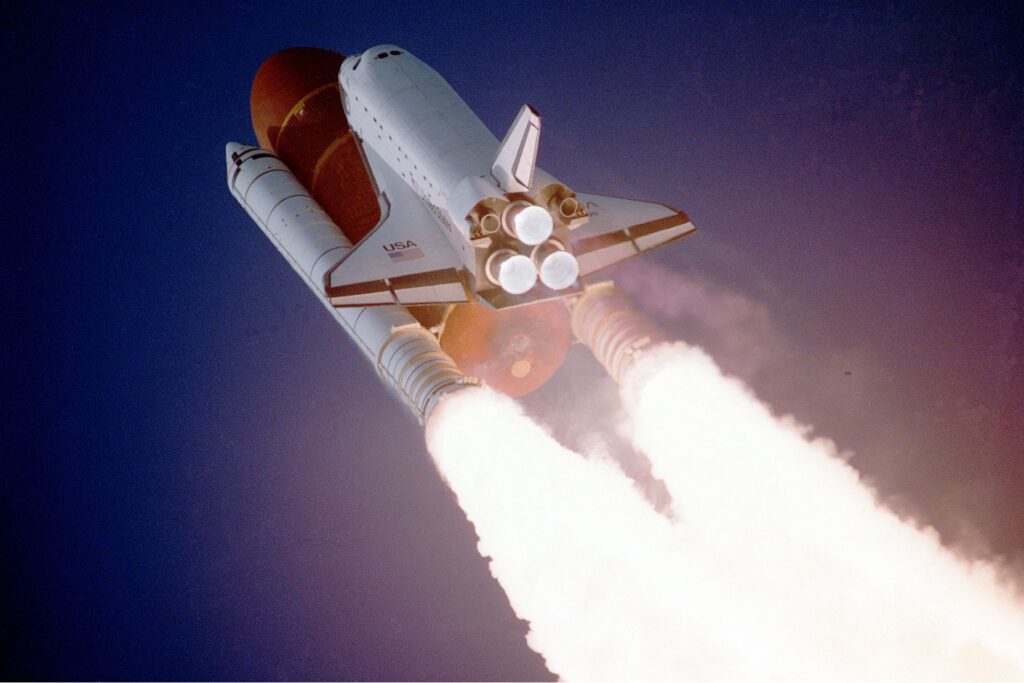
We provide high-performance AM solutions for critical applications in both the aerospace and defense industries. This includes propulsion, ballistics, and warheads.
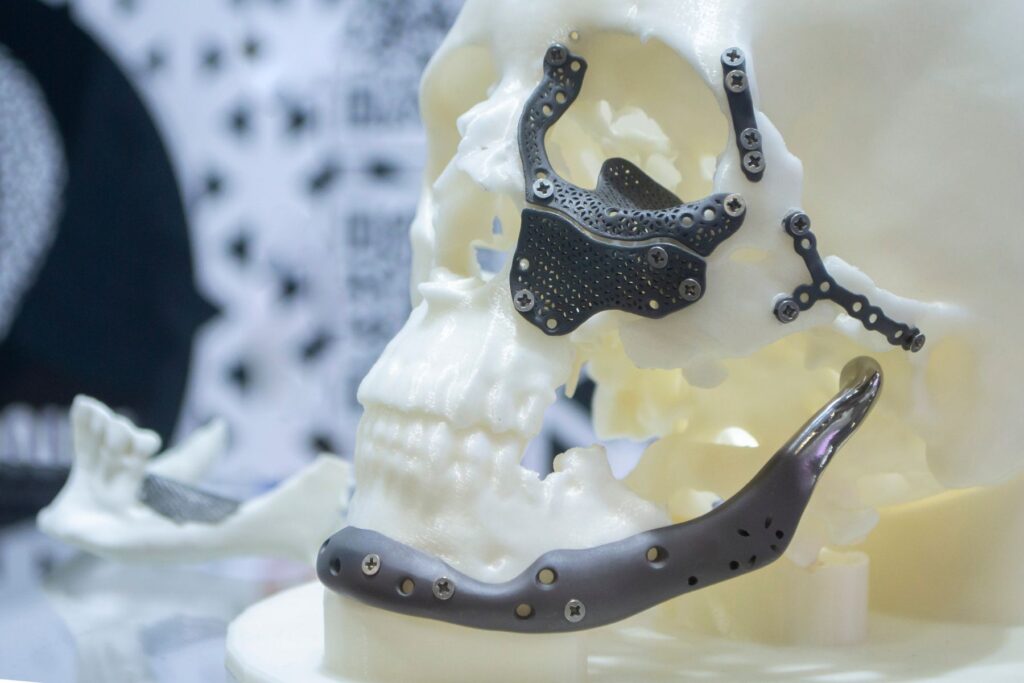
AM offers performance advantages for various medical applications. This is through its ability to enhance bone osteointegration, enhance implant design, and reduce overall part mass.
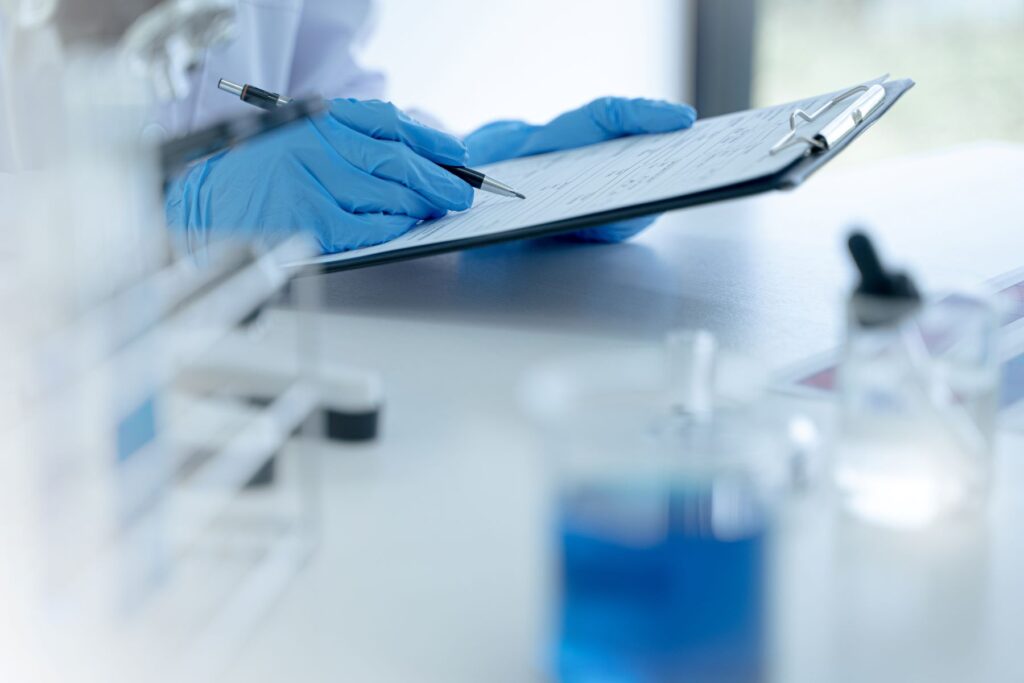
The corrosion resistance, durability, workability, and heat transfer properties of niobium make it ideal for challenging applications in the Chemical and Pharmaceutical industries.
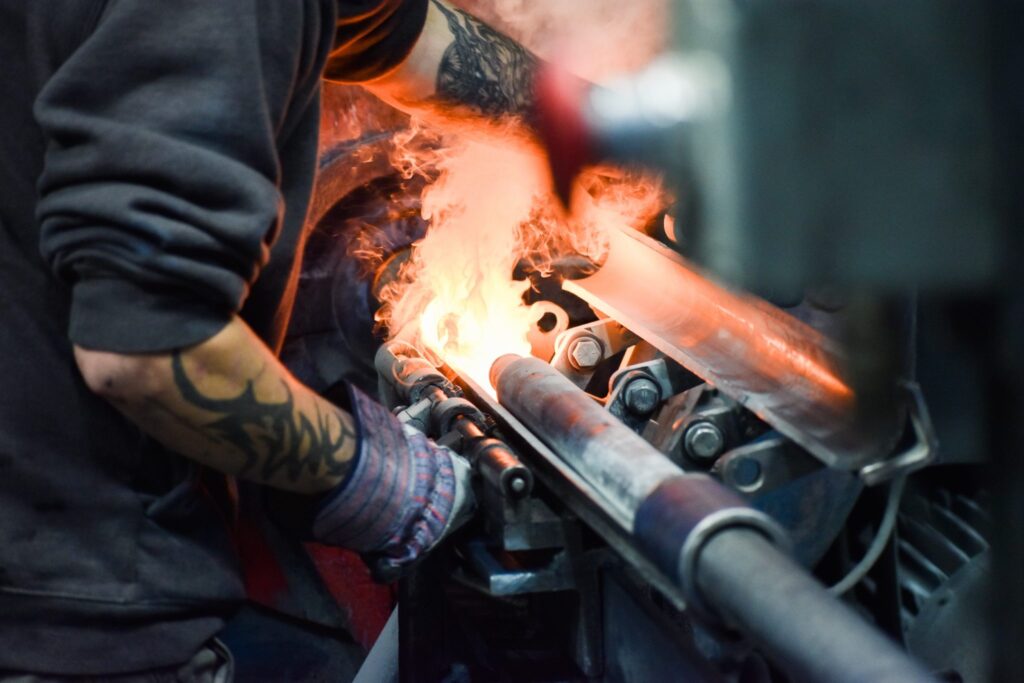
Today’s demanding applications in heat treating, sintering, brazing, annealing, metalworking, and other thermal processing areas require innovative AM refractory metal product solutions.
Properties of Niobium Powder for AM
Elmet’s powders for additive manufacturing are meticulously crafted to satisfy the stringent demands of additive manufacturing technologies, featuring properties that have consistently demonstrated effectiveness.
Purity | 99.95% |
Mean Particle Size D50 | 25-35 μm |
D10/D90* | 15/45 μm |
Bulk Density | 4 g/cc |
Hall Flow | 14-16 s/50g |
Oxygen | 1500 ppm |
Innovating the Future of Refractory Metals in AM
We are constantly expanding our portfolio and developing parts for markets yet to explore refractory metals. Our commitment to exceptional quality and performance makes us the ideal partner for even the most demanding applications of AM refractory materials.
As additive manufacturing (AM) advances across industries, Elmet stays at the forefront. Through ongoing research into new materials and applications, we help shape the next generation of advanced solutions.
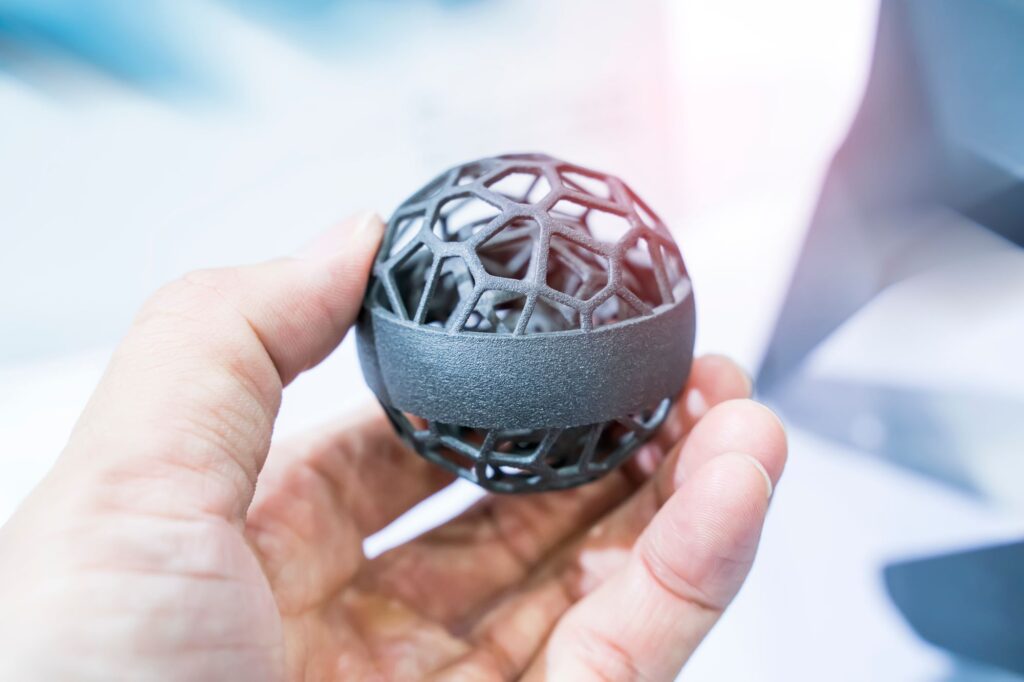
Materials for Additive manufacturing
Elmet Technologies’ core competencies of niobium, as well as tungsten, and molybdenum (in pure and alloyed forms), ensure our customers receive only the highest quality materials.
Our cutting-edge powder manufacturing technology, combined with our vertically integrated supply chain and metallurgical expertise, ensures the delivery of the highest quality materials for the most demanding applications and environments.
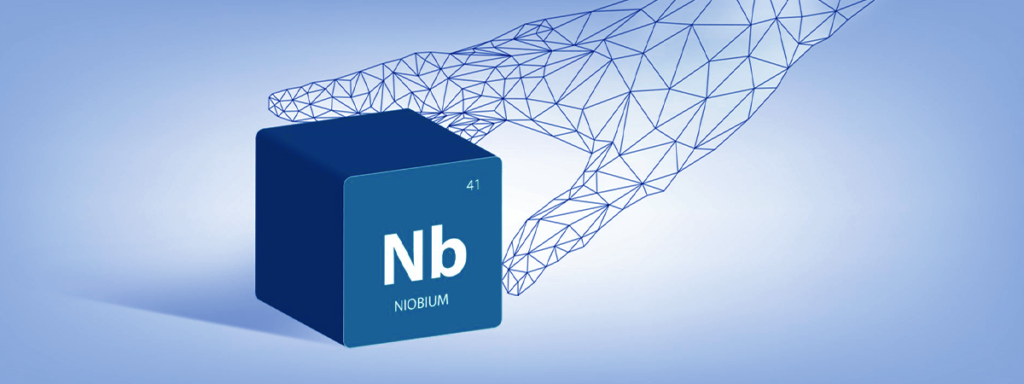
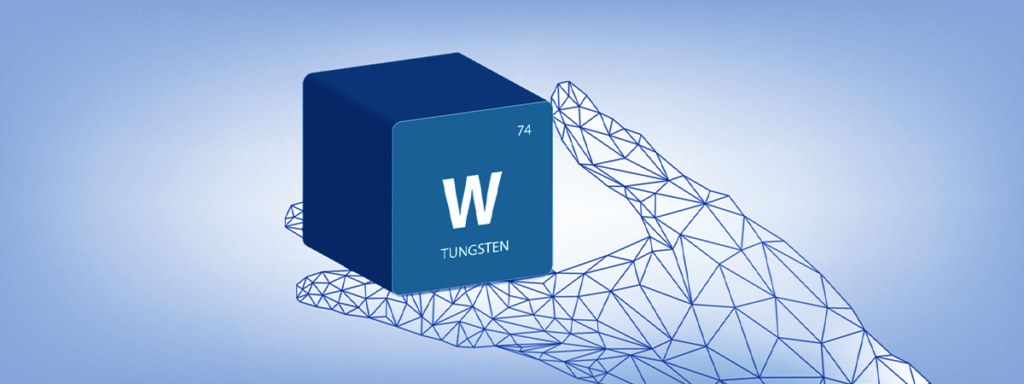
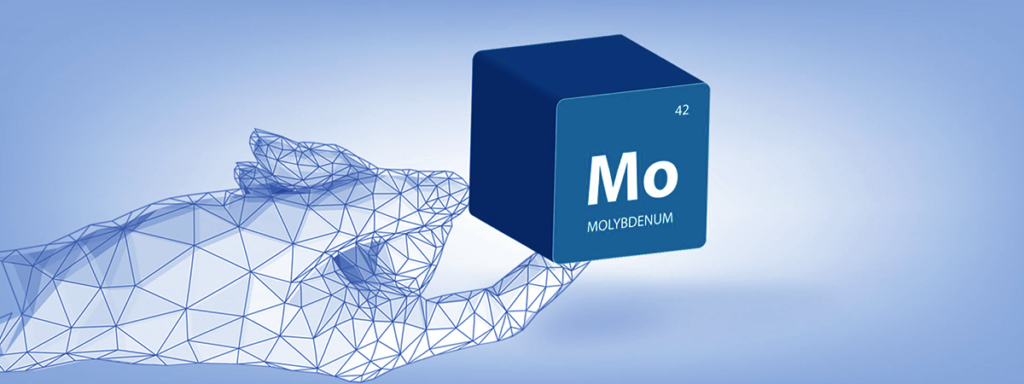
Furthermore, our advanced technological processes allow us to precisely customize our refractory metal feedstocks, thus achieving exceptional material properties and optimal performance for additive manufacturing. We design these powders specifically to meet the stringent requirements of the additive manufacturing industry.
Our metals’ properties exceed traditional production specifications and offer the following:
- High purity
- High bulk density
- Spherical powder morphology
- Exceptional flowability
- Low oxygen
- PSD optimized for specific printing methods
Methods of AM – Powder Bed Fusion
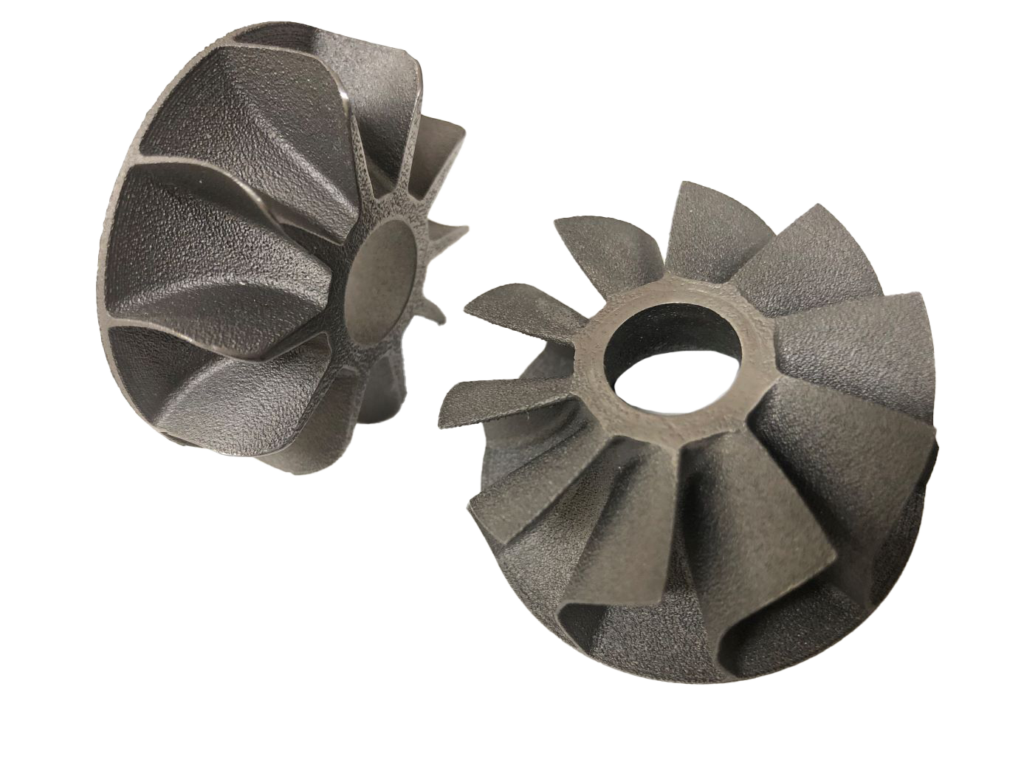
One of the most well-known additive manufacturing methods for metal parts is powder bed fusion. In this process, metal powders are spread in layers, and then laser or electron beam energy melts and fuses the material. As a result, this method efficiently creates complex metal components with precision.
This method not only saves costs but also minimizes material waste through its efficient resource usage. At Elmet, we specialize in crafting custom powders and optimizing printing parameters. We manufacture high-density refractory metal components tailored for various applications