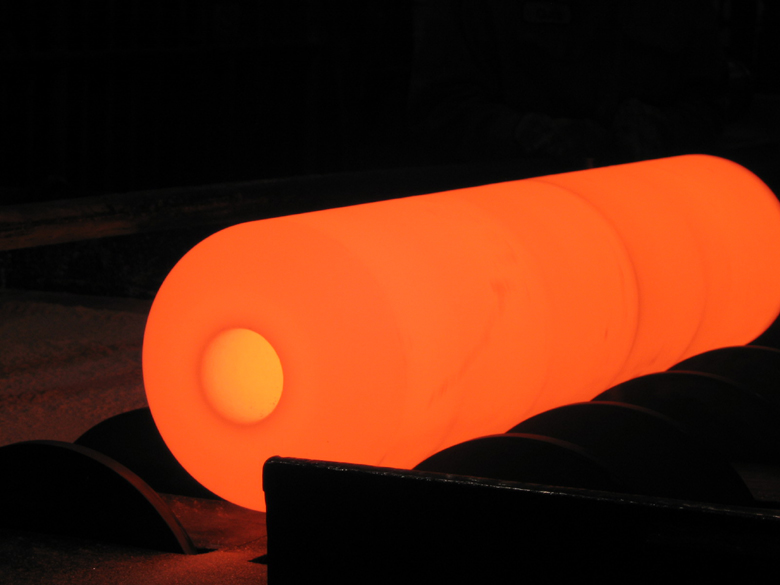
Niobium Billets
Elmet Technologies is a trusted leader in transforming niobium billets into high-quality, reliable materials for industries such as defense, aerospace, energy, and manufacturing. By working with both commercial and nuclear-grade niobium billets sourced from reputable Western suppliers, we leverage advanced extrusion and rolling processes to create rods, plates, and sheets that meet the highest standards.
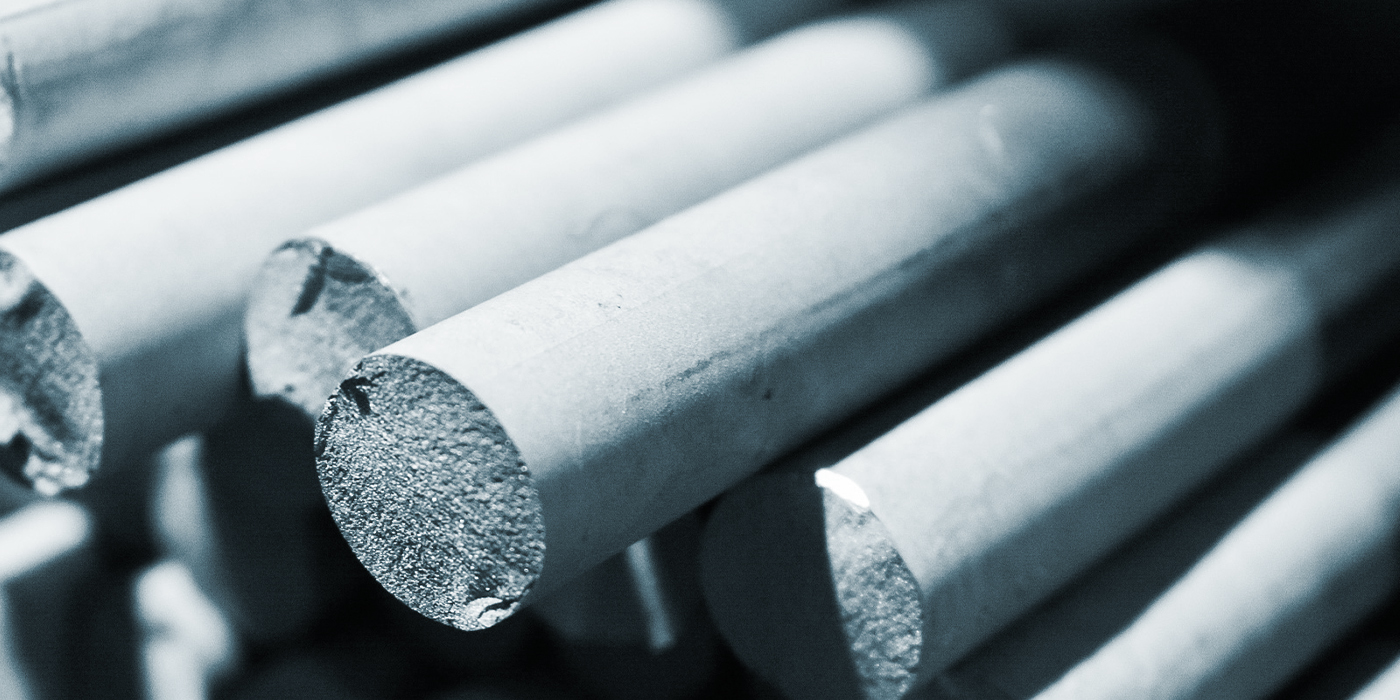
Our skilled team of engineers, production specialists, and customer service professionals are dedicated to helping you meet your specific material, design, and process requirements with precision and efficiency.
Niobium billets offer several key advantages over other manufactured forms:
- Cost-effective production
- Exceptional precision in manufactured parts
- Superior structural integrity
- Faster lead times for finished parts
At Elmet Technologies, we deliver unmatched expertise and quality to ensure your projects succeed. Let us assist you with your niobium material needs today.
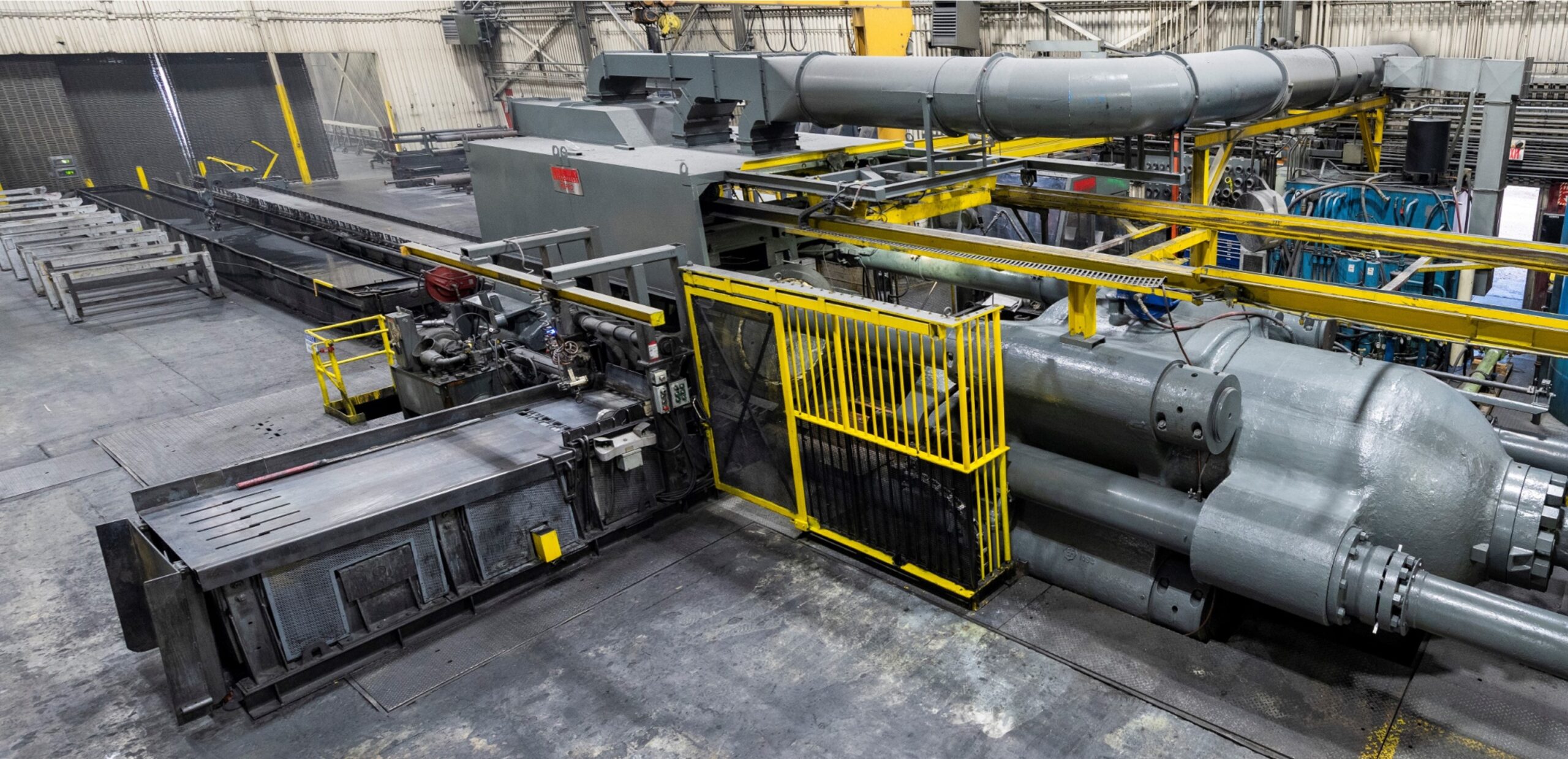
Extrusion of Niobium Billets
Our Elmet facility in Coldwater, MI manufactures high-quality niobium sheets and plates using advanced extrusion and rotary forge technology. Starting with niobium billets from trusted Western suppliers, we extrude and roll the metal to meet precise customer specifications. We also provide finishing processes like heat treatment, cleaning, straightening, machining, and cutting to ensure our products are ready for any application.
Our state-of-the-art, 5,500-metric-ton extrusion press efficiently shapes rods, tubes, and complex cross-sections in diameters ranging from 152–432 mm (6–17 in). The process begins by preheating billets to temperatures as high as 1,925°C (3,500°F) using either gas-fired or inert atmosphere induction furnaces, ensuring optimal material performance and quality.
Advanced Hot and Cold Rolling
Numerous industries depend on hot and cold rolling procedures as an integral component of their manufacturing processes. At Elmet, we house a wide selection of mill sizes, designed to produce sheets of varied sizes. Not only can we adjust for unique dimensions, but we can also manipulate sheet thicknesses to facilitate the creation of niobium, along with an array of other refractory and specialty metals.
Moreover, we own and operate a sizable cold rolling infrastructure, equipped to conduct multiple annealing or rolling cycles. This equipment harnesses 3 million pounds of force, which is utilized to convert thick ‘sheet bars’ into plates. Our team consists of process engineers and production developers who specialize in both hot and cold rolling methods.
Understanding the optimal rolling conditions and parameters for specific sheets is a fundamental aspect of their knowledge. Achieving the desired surface quality and yielding successful results hinge on this understanding and the accurate pre-processing of materials.
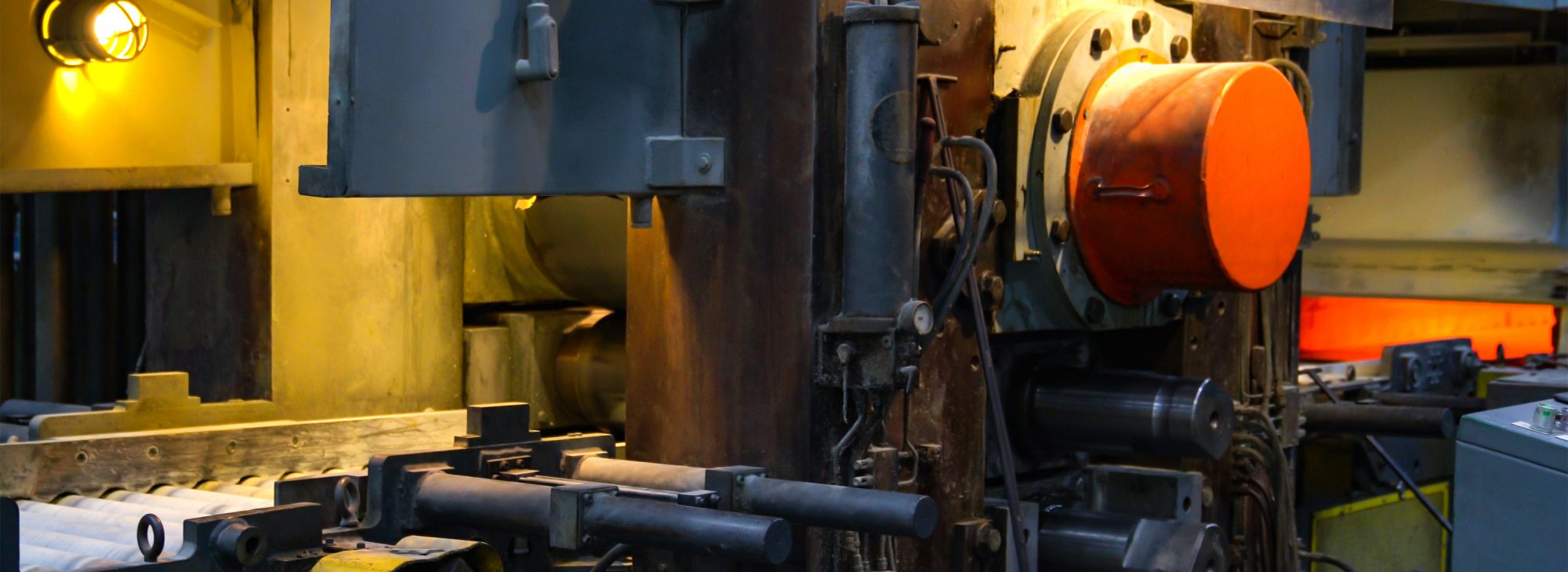
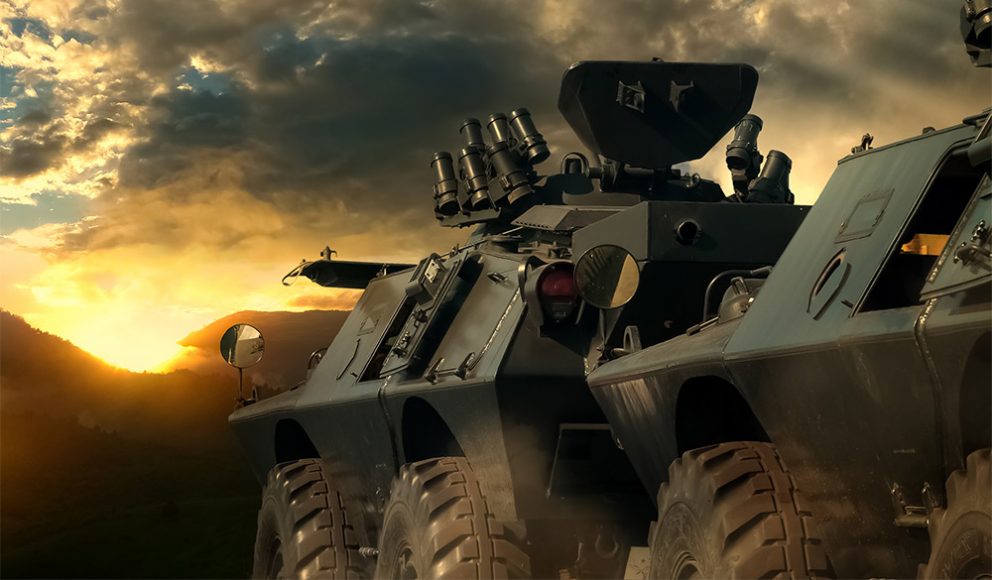
Niobium for Defense Applications
Military and defense contractors rely on Elmet for its unmatched expertise in producing high-performance components made from molybdenum, tungsten, and their alloys.
These critical materials are essential for high-stakes applications, especially in areas like national security. To ensure the highest standards, Elmet adheres to rigorous quality control processes, delivering products that meet even the most demanding specifications.
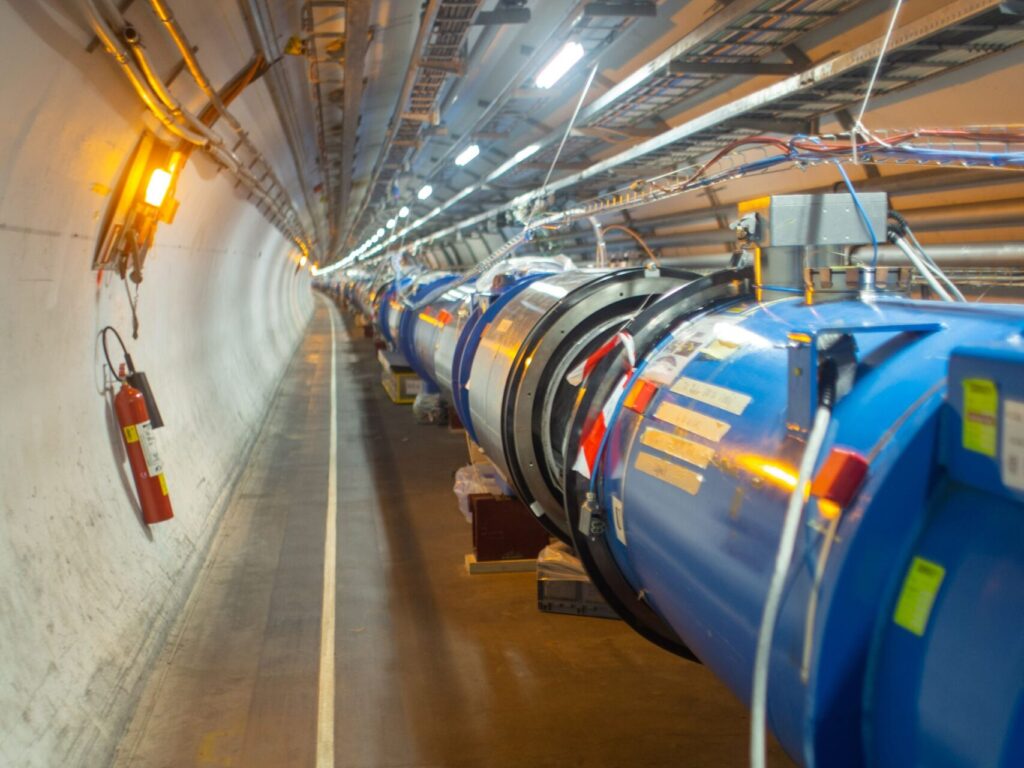
Niobium for Superconducting
Niobium plays a crucial role in the development of high-temperature superconducting alloys, such as niobium-tin (Nb3Sn) and niobium-germanium (Nb3Ge).
These advanced materials are essential for creating superconducting magnets used in analytical chemistry applications, including MRI and NMR machines. Furthermore, the Large Hadron Collider at CERN relies on niobium-titanium magnets to guide high-energy particles through its beamline with precision.