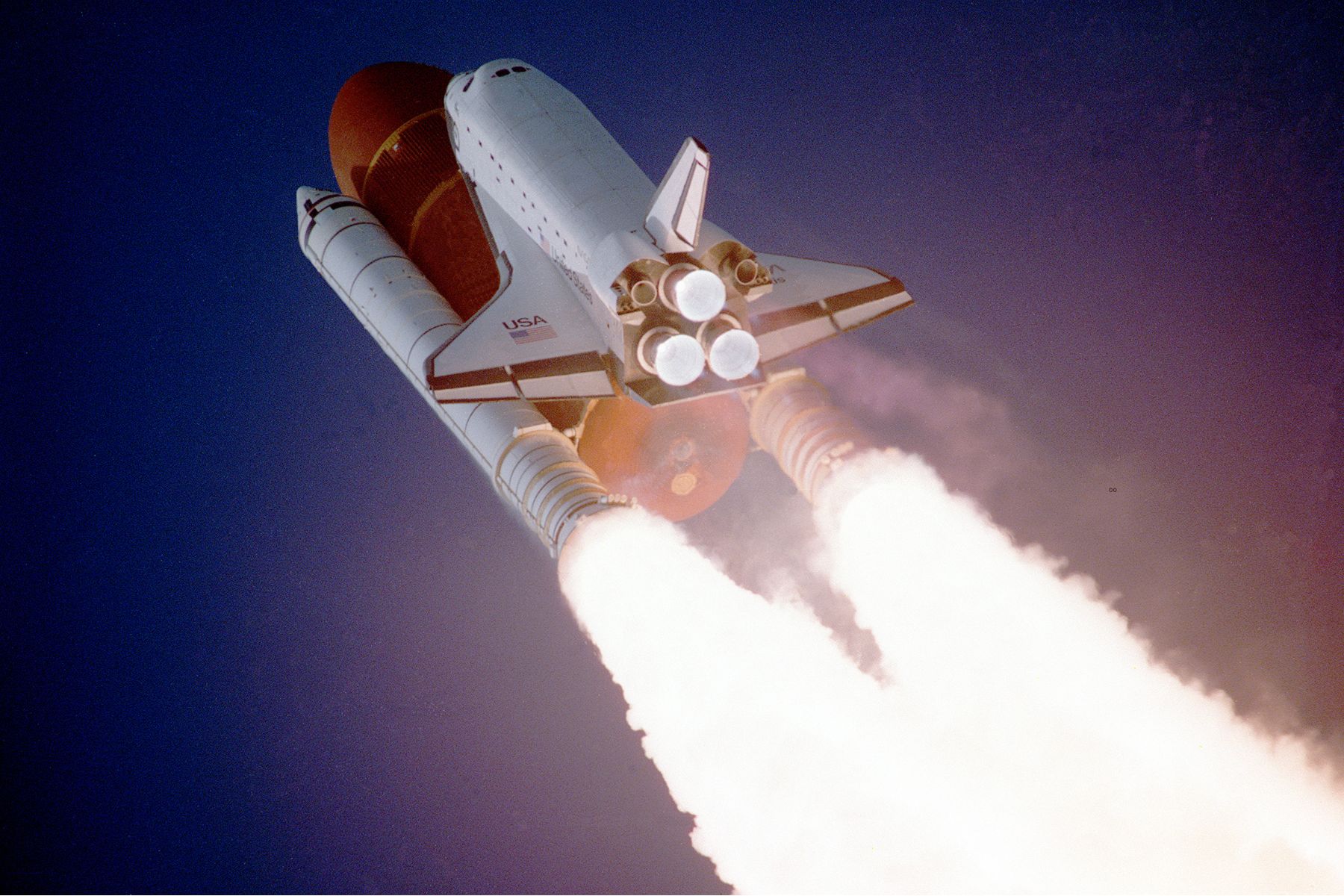
Niobium-Based Alloys for Rocket Nozzles
Elmet Technologies is a leading manufacturer of niobium-based alloys for rocket nozzles. They are undoubtedly vital for aerospace solutions. Building machines that fly through our atmosphere or explore space requires materials capable of withstanding rapid and extreme changes in mechanical load and temperature.
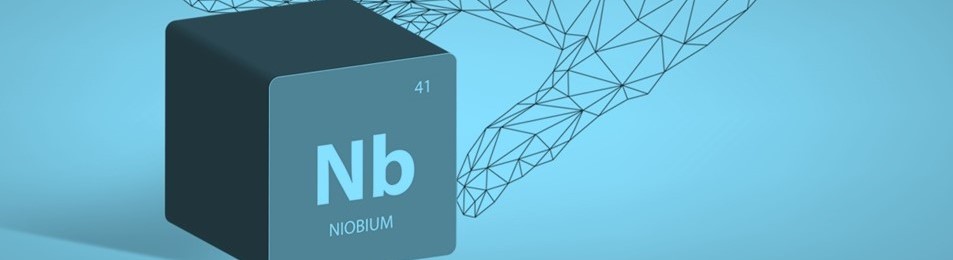
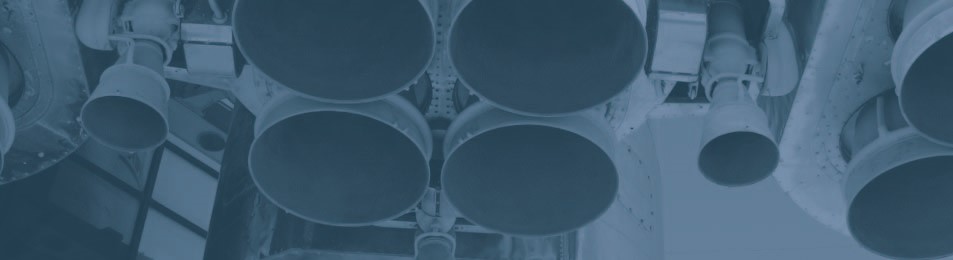
By alloying niobium, hafnium, and titanium, manufacturers create Niobium C103, an alloy that can be extruded into bars or powders. These forms are perfect for additive manufacturing of complex rocket and jet propulsion components. Consequently, these advanced alloys are ideal for use in spacecraft and launch vehicles, given their exceptional performance characteristics.
At Elmet, we focus on manufacturing high-purity refractory metals and alloys for harsh operating environments, offering a choice of industry-trusted products for aerospace and defense.
the clear Choice for Rocket Nozzle Manufacturing
A key advantage of the niobium alloy is its high strength at temperatures up to 2700 °F (1482°C), particularly in high performance rocket nozzle applications.
In addition, Elmet Technologies C103 niobium alloy has excellent resistance to high-frequency vibrations at cryogenic temperatures, as occurs in many satellite applications, due to its low ductile-to-brittle transition temperature.
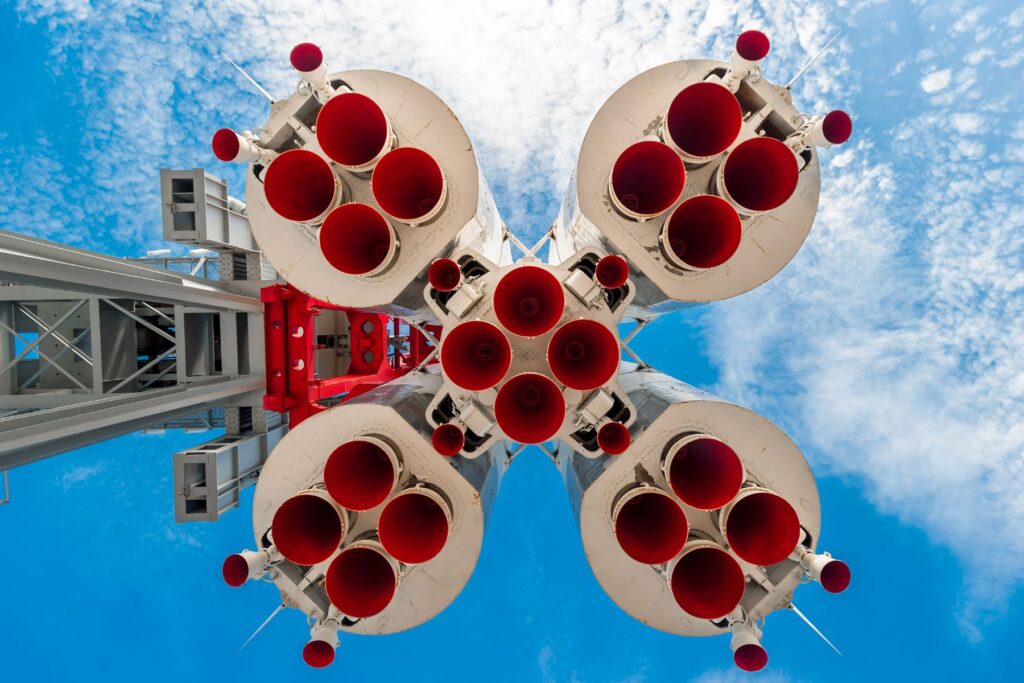
Benefits of Using Niobium-based Alloys for Rocket Nozzles
- Capabile of withstanding high stresses at elevated
temperatures - Low ductile-to-brittle transition temperature for cryogenic
applications - Formable after TIG welding
- Excellent fabricability
- Readily weldable
C103 Niobium Alloy
C103 niobium alloy is a complex refractory alloy consisting primarily of niobium. Added in are 10wt% hafnium, 1wt% titanium, and trace amounts of other elements. The key to its success is its low density and exceptional strength across a very wide temperature range (from cryogenic temperatures up to 1482 C4). C103 has been a trusted material since the early days of the space age. Its proven performance and reliability make it one of the top refractory metals used in propulsion and space exploration technologies
C103 stands out for its ease of formation, unlike many refractory metals, ceramics, or composites. Regardless of its high melting point, it can undergo hot, warm, or cold work seamlessly. Consequently, traditional techniques become capable of producing both flat and round products efficiently. Moreover, C103 showcases remarkable machinability and can be TIG welded without suffering a significant loss in ductility. This particular advantage paves the way for the uncomplicated fabrication of complex aerospace components.
C103 is used in a variety of aircraft components, from thrust augmenter flaps in gas turbines to high-temperature valves. Research is currently underway to develop niobium-based alloys for next-generation aerospace technologies. This includes heat pipes to dissipate heat from hypersonic leading edges and nose cones.
Available Forms of C103 Niobium Alloy
Elmet collaborates with customers to fabricate and machine niobium for rocket nozzles and other components for aerospace. This includes build-to-print and design C103 niobium alloy components. All C103 meets ASTM B652, B654, B655, AMS7852 and AMS7857 specification.
Niobium (Nb) C103 Material | Dimensions (inches) | Dimensions (cm) |
---|---|---|
Bar & Rod | 1.5 in. – 6.5 in. diameter | 3.81 cm – 16.51 cm |
Sheet | 0.024 in. – 0.1875 in. thick, up to 24 in. width | .06 cm – .48 cm, up to 61 cm width |
Plate | 0.1875 in. – 1 in. thick, common widths | .06 cm – 2.54 cm |
Ingots | up to 9.5 in. diameter | |
Slabs | As requested | |
Nb C103 Powder | Additive manufacturing | |
Fabricated Parts | Per customer specifications |