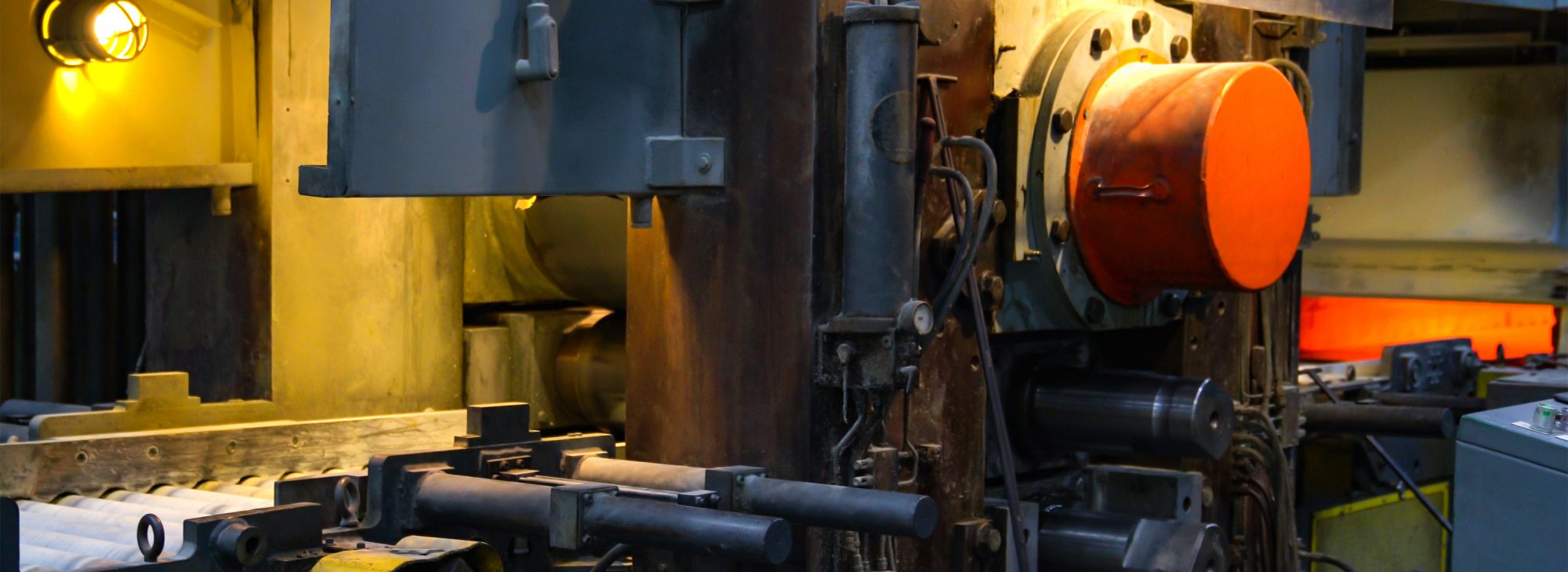
Niobium Sheet and Plate
As a global leader in refractory metals, Elmet Technologies provides niobium sheet and plate with a cold-rolled and chemically cleaned surface. Due to their strength and workability, very thin sheets can be clad to other surfaces, offering superior corrosion protection and cost-effectiveness. Each sheet and plate undergoes thorough visual inspections to identify issues like slivers, laminations, excessive roll marks, and handling scratches. Technicians also condition localized defects as needed, ensuring consistent thickness tolerance.

At Elmet Technologies, we understand that product quality is key to our customers’ success. That’s why every step of our production cycle is carefully monitored. Our rigorous quality programs are designed to consistently deliver reliable, high-quality products.
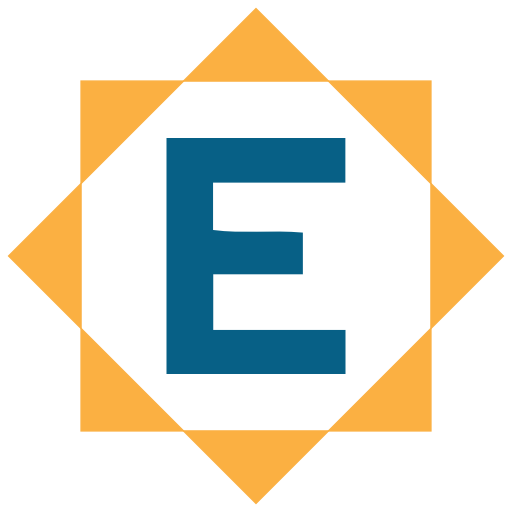
Our team of highly qualified technical experts has material knowledge and application expertise. Products and processes are developed upon customers’ demands. All our plants are ISO 9001 certified, and we comply with all customer approval processes.
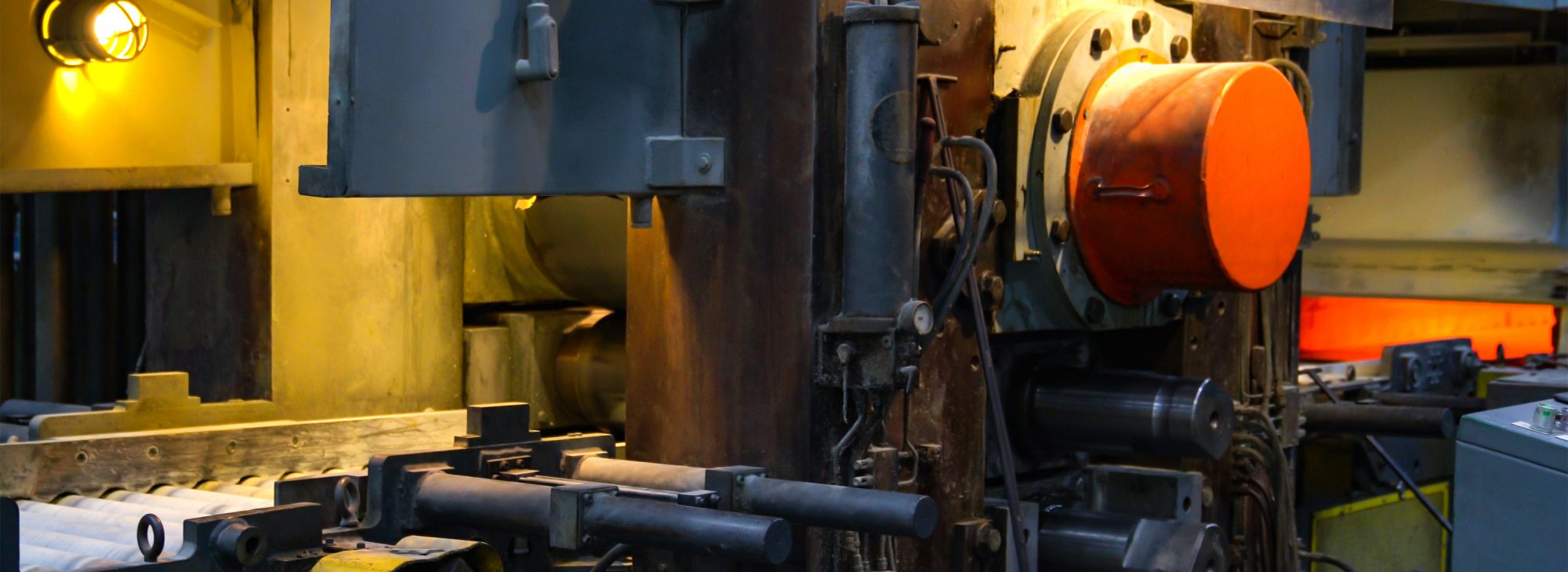
Niobium sheet and Plate Cold Rolling Services
Moving from selecting the perfect material for your application to transforming it into its final form can be a complex and challenging process. That’s where Elmet Technologies comes in. Our team of expert process engineers and production specialists excels in both hot and cold rolling techniques, and ensuring precision and excellence every step of the way.
Initially, we procure both commercial and nuclear-grade niobium billets from reliable Western sources. Following this, we employ both extrusion and rolling processes to fabricate rods, plates, and sheets. The knowledge of correct rolling conditions and parameters is critical to achieving the desired surface quality on the sheet. Accurate pre-processing of materials significantly influences the final outcomes and is of utmost importance.
Materials & Specifications
At Elmet, we proudly use over 9 rolling mills across our locations. We can provide a range of mill sizes to create a variety of sheet thicknesses for a range of refractory and specialty metals. There is also a large cold rolling operation offered that uses several annealing/rolling cycles to apply 3 million pounds of force to transform thick ‘sheetbars’ into plates. Sheets can range from 3 inches – .013 inches in thickness. Our customer service team is happy to discuss custom solutions for the right project.
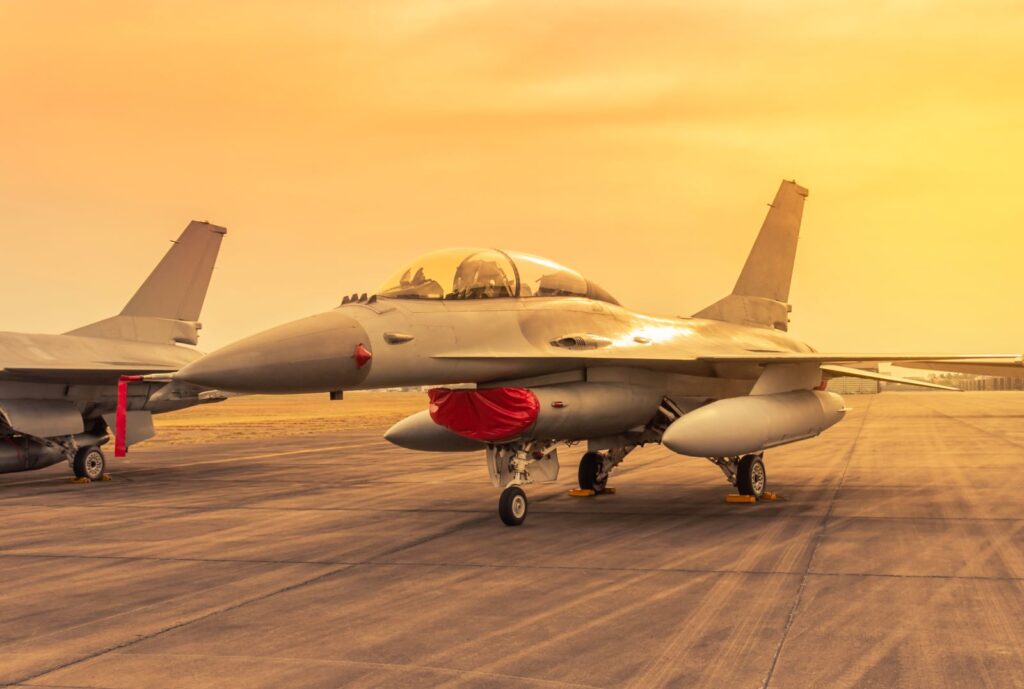
Applications
Electronics, aerospace, energy, and defense manufacturing are all applications that use the unique properties of these materials.
These metals are widely used in processes like vacuum deposition for metallization, offering unmatched thermal stability and resistance to shock.
Their durability enables the production of components with extended lifespans, ultimately reducing operational costs and enhancing efficiency.
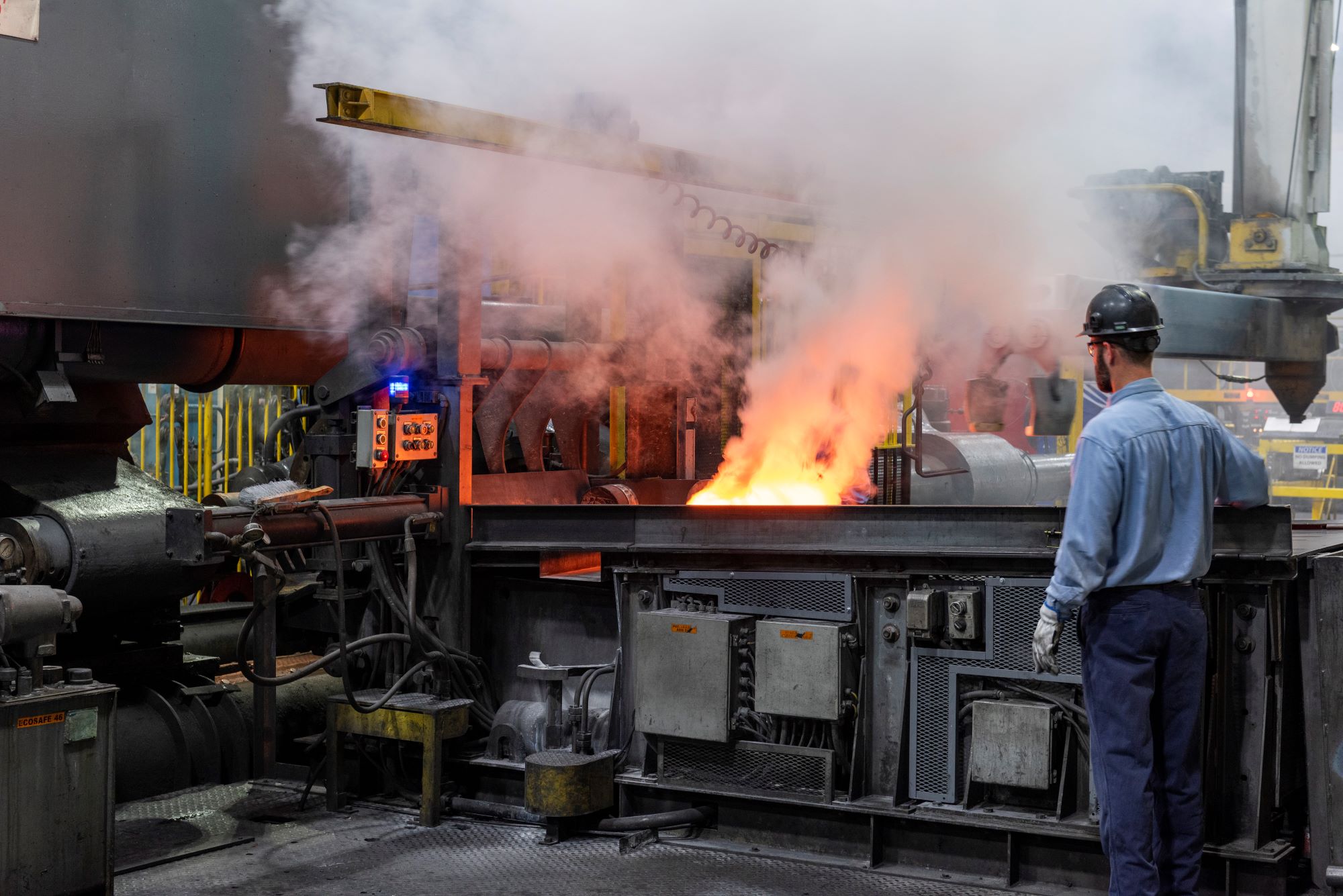
Toll Services
Many industries rely on hot and cold rolling processes as part of their manufacturing. Typically, whether this is for recycled metal powders or ‘fresh’ materials, starting materials are in the form of thick ‘sheetbars’.
Cutting and manufacturing these sheetbars is difficult, so manufacturers use hot or cold rolling to create thinner sheets for directly cutting shapes and objects.
This avoids damaging or dramatically altering the desirable properties of the refractory or specialty metal.
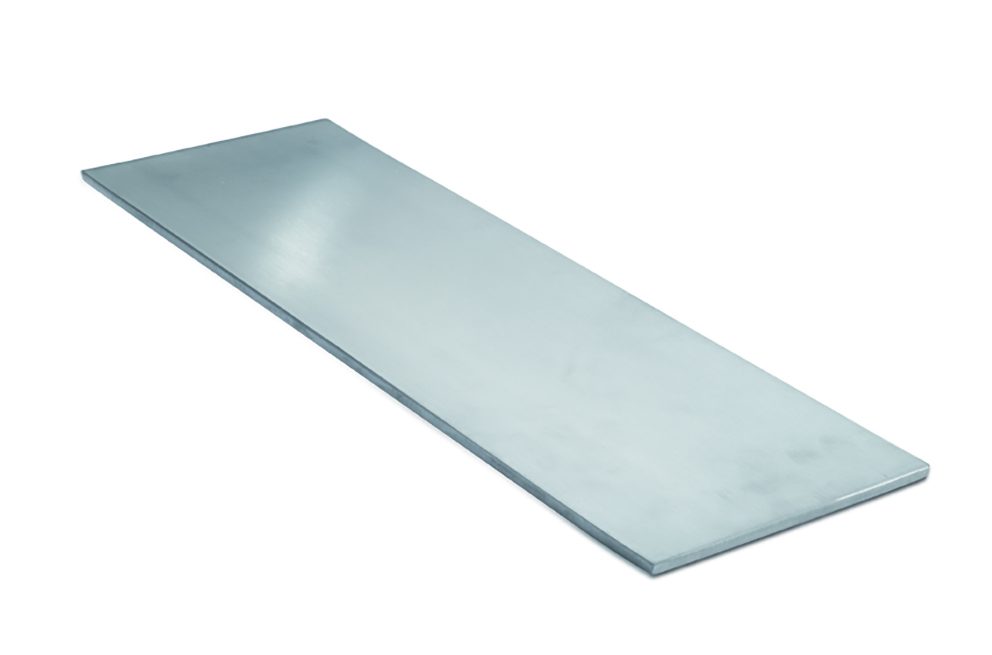
Offering Plates and Sheets in Additional Refractory Metals
- Molybdenum
- Lanthanated Molybdenum
- Tungsten
- Tungsten Heavy Alloy
- Titanium, Zirconium, Molybdenum Alloy (TZM)